Mobile Robotics:
The Technology Behind Our AMRs
The Different Operating Modes of Our AMR Robots to Meet Your Needs
Our AMR robots offer three operating modes to adapt to every situation: an autonomous mode for completely independent navigation, a follower mode to accompany your operators in their movements, and a remote-controlled mode for manual control. This flexibility ensures optimal use according to your needs.
Advanced Localization and Navigation Algorithms
for Optimal Precision
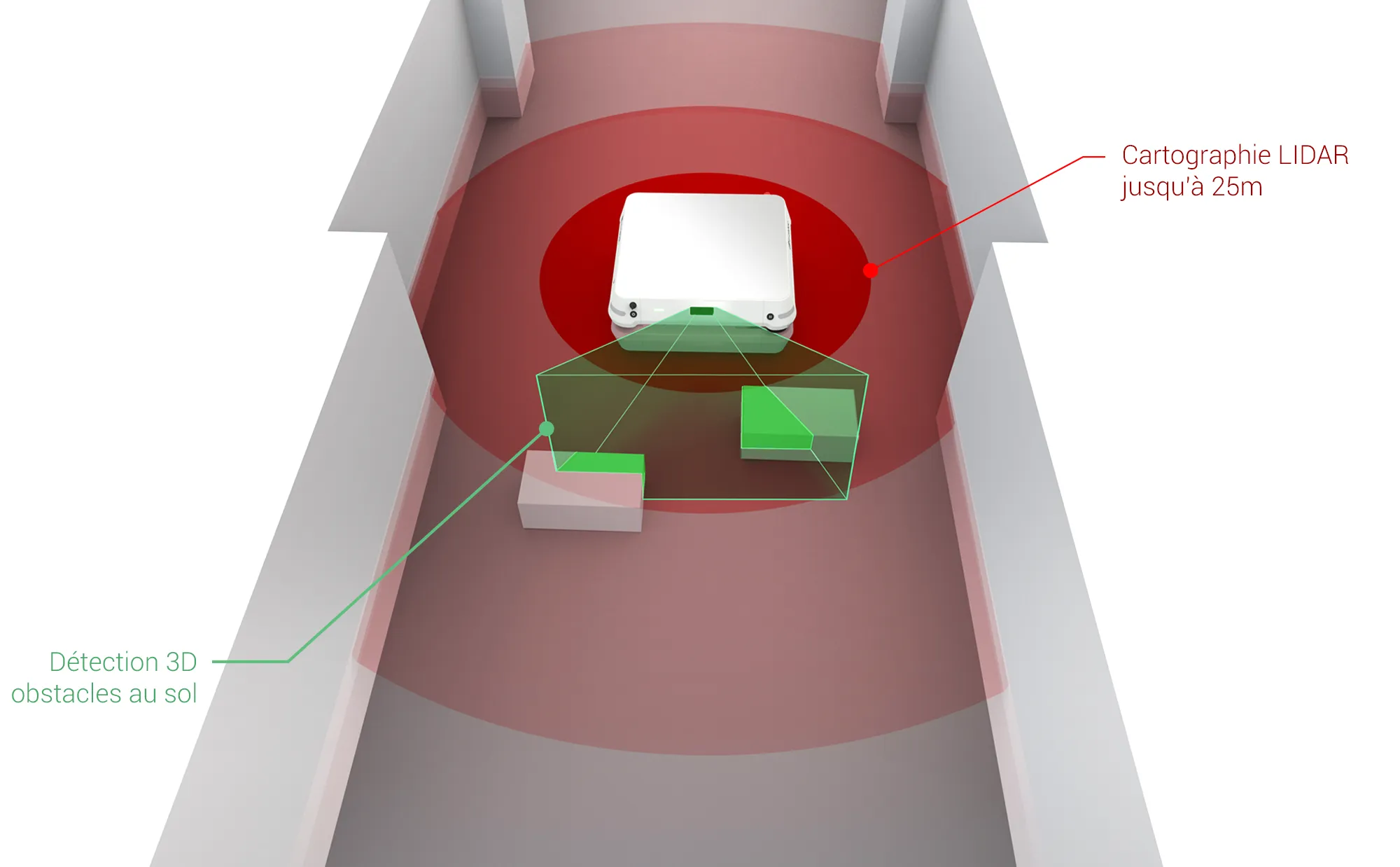
Precise Localization with High-Performance Sensors
Our AMRs use localization algorithms based on advanced sensors, such as LIDAR, cameras, inertial measurement units (IMU), and motor encoders. With these technologies, our mobile robots map their environment in real-time, without the need for fixed infrastructure like magnetic strips or floor markers.
As a result, they can localize themselves within their environment and know exactly where they are at any given moment in the factory or warehouse, ensuring precise localization for all their tasks.
Smart and Adaptive Navigation for Better Efficiency
Our AMRs benefit from optimized navigation thanks to the integrated artificial intelligence of MyCobot OS. This advanced software enables the mobile robots to move efficiently in dynamic and complex environments.
Our robots are capable of avoiding static and dynamic obstacles, such as machines or moving operators, while respecting predefined safety zones. Their ability to instantly recalculate trajectories ensures smooth navigation. This adaptive intelligence guarantees safe coexistence with humans, making AMRs an ideal solution to optimize logistics flows while maximizing productivity.
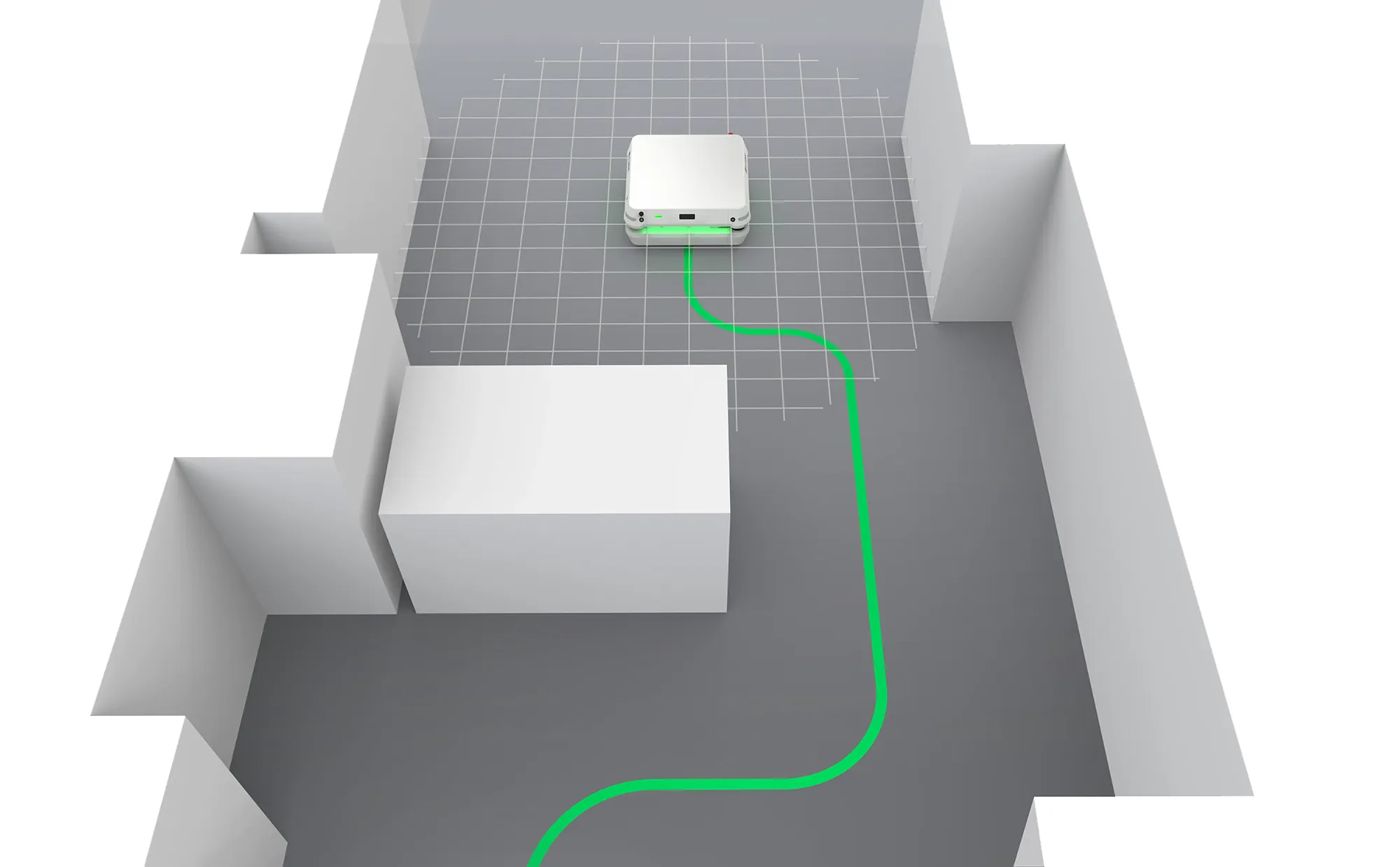
A Secure Mobile Robot with Programmable
Protection Zones Around the Product
To ensure workplace safety, our mobile robots are equipped with programmable safety scanners. These scanners define three distinct zones around the robot: the free zone, where no restrictions are applied; the orange zone, where the robot slows down to better anticipate risks; and finally, the red zone, where the robot stops immediately, equivalent to an emergency stop.
Thanks to these safety zones, the robot avoids any contact with people and obstacles, ensuring smooth and secure cohabitation in industrial or logistical environments.
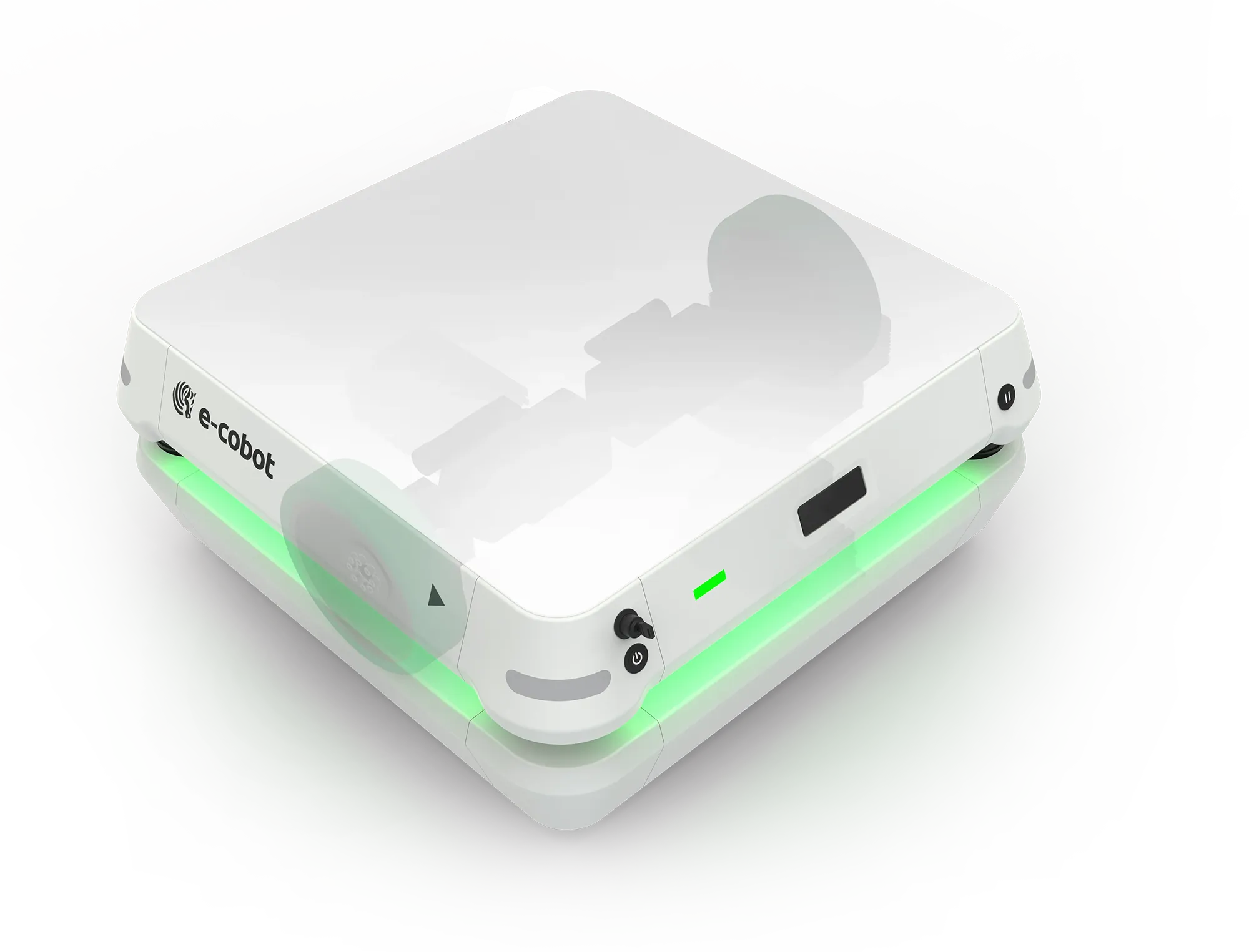
A precise and responsive motorization for reliable navigation
The motorization of our mobile robots is both robust and responsive, providing optimal performance in various environments. This motorization system is perfectly integrated with our navigation algorithms, allowing the robot to adjust its speed based on the tasks to be completed and the surrounding conditions. Additionally, safety encoders are used to ensure that each command sent to the robot is executed with precision.
These encoders, combined with an odometry system, also enable the robot to calculate its exact position within its environment, contributing to reliable and continuous localization throughout its movements.
Optimized energy management for flawless autonomy
The energy management of our mobile robots relies on high-performance LFP (lithium iron phosphate) batteries, providing great autonomy and a long lifespan.
With an intelligent consumption management system, our robots can adapt in real-time to their energy needs. In case of low battery or periods of inactivity, the robot automatically recharges, ensuring continuity in logistical flows without the risk of failure. This enhanced autonomy guarantees optimal efficiency throughout its work cycles.
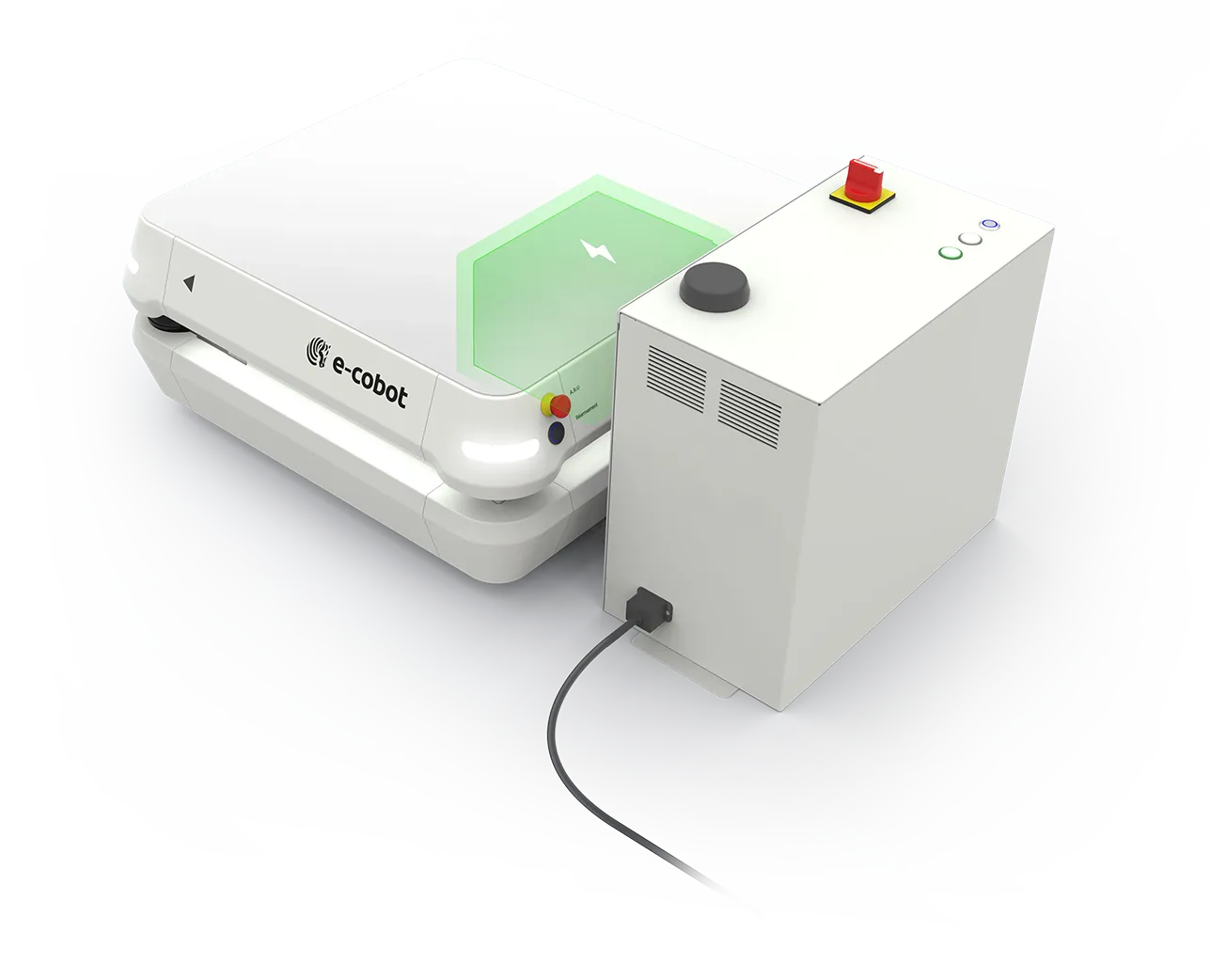